
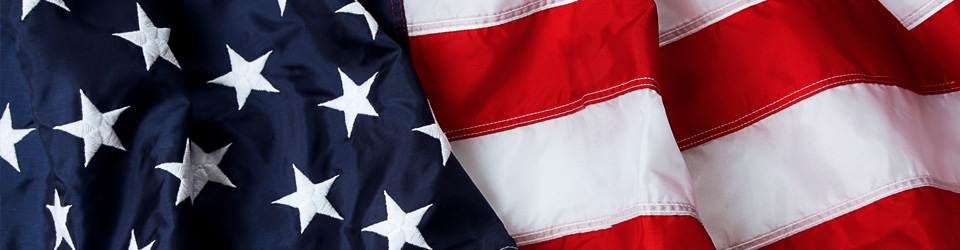
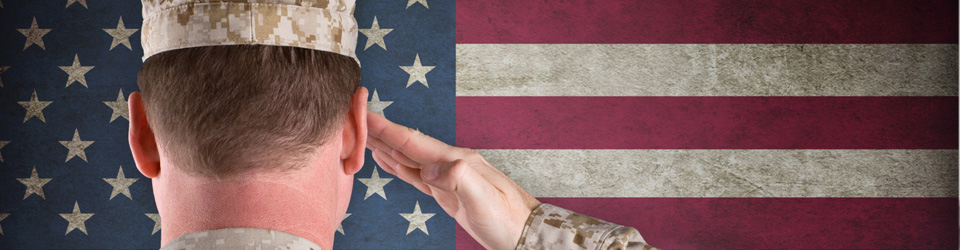
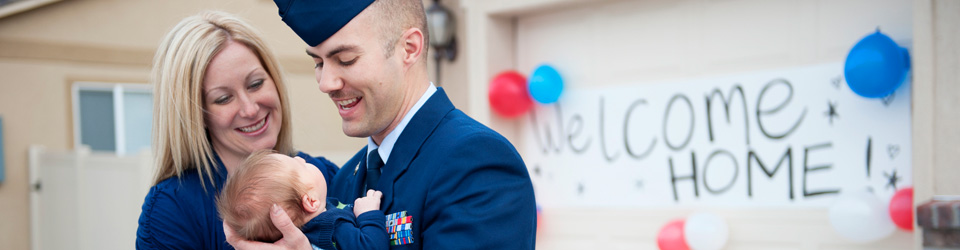
Job Information
Panasonic North America Facilities Maintenance and Reliability Manager in De Soto, Kansas
Overview
We are proud to announce the establishment of a state-of-the-art Li-ion battery factory, set amidst the beautiful Kansas City Metro. This groundbreaking green-field factory will serve as a pioneering hub for innovation in sustainable energy solutions.
Responsibilities
Summary: We are proud to announce the establishment of a state-of-the-art Li-ion battery factory, set amidst the beautiful Kansas City Metro. This groundbreaking green-field factory will serve as a pioneering hub for innovation in sustainable energy solutions.
If you are passionate about contributing to a sustainable future and being part of a dynamic team shaping the electric vehicle revolution, this opportunity is tailor-made for you. We are seeking dedicated individuals to join us as full-time, on-site team members at our new, state-of-the-art factory located in the thriving city of DeSoto, Kansas.
Position Summary: We are seeking a highly experienced and detail-oriented individual to join our dynamic team as the Facilities Maintenance and Reliability Manager. This role will lead the Facilities Maintenance and Reliability Team and the development and execution of asset maintenance and reliability programs for our Facilities infrastructure. In this role, you will be responsible for building the Team, developing a fully integrated asset care strategy, and implementing a systemic approach to maximize our Facilities assets.
Essential Duties:
Builds, leads, and develops the Facilities Maintenance and Reliability Team (16+ personnel) to ensure maintenance and reliability excellence and excellent customer service. The team will consist of:
Maintenance Supervisors (Direct Reports)
Maintenance Technicians (I, II, and III levels) (Indirect Reports)
Reliability Technicians (I, II, and III levels) (Indirect Reports)
Maintenance Planner(s)
Reliability Engineer(s)
Champion best practices, company policies, and service excellence standards.
Oversee development, implementation, and adherence of/to procedures, work instructions, and best business practices.
Support Maintenance Supervisors in determining staffing requirements, work assignments and schedules, and oversee maintenance cost, risk, and audit activities.
Create and manage Facilities Maintenance and Reliability budgets (both operational and capital expenses).
Collaborate with Operational Excellence/Continuous Improvement Team in the development and execution of the Facilities Maintenance and Reliability program.
Ensure development, maintenance, and reporting of metrics with respect to safety, quality, cost, delivery, and people for the Facilities Maintenance and Reliability Team.
Create standardized reporting metrics/KPIs to monitor maintenance and reliability performance of key facilities equipment and systems.
Ensure that monthly statistical information is compiled, verified, and reported to management regarding maintenance and reliability trends.
Champion ongoing execution of RCAs, ACAs, and FMEAs.
Oversee and implement world-class asset maintenance strategies to optimize equipment efficiency and improve equipment operating and maintenance costs.
Ensure a robust preventive maintenance program and leverage predictive maintenance tools where applicable.
Identify critical spare parts and oversee proper spare parts management.
Collaborate with other site Maintenance and Reliability leaders to ensure efficient utilization of spare parts inventory across factory sites, driving network spares inventory optimization.
Build a network with other site Maintenance and Reliability leaders to strengthen knowledge and capability through best practice sharing and personnel training/development.
Own development of the Facilities asset maintenance and upkeep masterplan to ensure lowest possible asset lifecycle costs.
Work closely with Facilities Operations Team to provide technical expertise, strategic guidance, and overall coaching for success.
Train and deploy TPM methodologies across the Facilities organization.
Ensure upkeep of accurate maintenance records for Facilities assets and full utilization of Facilities CMMS.
Drive OEE improvements through improved execution of the Maintenance and Reliability program. This includes significant analysis of CMMS data.
Responsible for conducting, documenting, and reporting periodic inspections, measuring effectiveness, efficiency and resiliency of maintenance and reliability strategies for facilities equipment and systems with the goal of minimizing unplanned downtime, anticipating problems, and solving facility issues.
Actively participate in problem-solving strategies and provide to upper management recommendations for reliability and efficiency improvements, and other improvements to minimize system downtime.
Align with Facilities Engineering, Operations, Construction, and Design Teams to provide user requirements concerning maintenance and reliability for development of project scopes.
Ensure compliance with all regulatory requirements in areas including safety, quality, and finance.
Partner with EHS to provide support with Safety Policy and Compliance.
Partner with HR to provide support with New Employee Orientations, Interviews, and Recruiting/Networking events.
Support the development and professional growth for all team members, conducting constructive performance reviews and development dialogues.
Leads and participates in/on a variety of meetings, committees, task forces, and/or other related groups to solve specific problems as well as to communicate information regarding services, programs, areas of opportunity, and/or other pertinent information as appropriate.
Dependent upon workload, this position may on occasion be required to assist with other duties related to the department, in addition to primary responsibilities of leading Facilities Maintenance and Reliability Teams, under the supervision of the Director or Facilities.
Personal Protective Equipment (PPE) Requirements:
- To ensure the health and safety in the workplace and for the protection of our employees’, wearing PPE is a possibility and includes equipment such as a full Tyvek suit, safety shoes, gloves, safety glasses, face mask, and a full hazmat suit that includes a respirator.
The foregoing description is not intended and should not be construed to be an exhaustive list of all responsibilities, skills and efforts or work conditions associated with the job. It is intended to be an accurate reflection of the general nature and level of the job.
Qualifications: Requirements - Required and/or Preferred
Education
- Basic/Required: Bachelors in engineering or relevant field of study
Essential Qualifications
10+ years of experience in maintenance and reliability management
Proven experience with building and sustaining successful Reliability Centered Maintenance (RCM) programs.
Skills and experience necessary to satisfy the required “Essential Duties”.
Proven leader with a strong work ethic and a “get-the-job-done” approach, who consistently delivers excellent customer service, both internally and externally.
Excellent analytical and problem-solving skills, with the ability to identify root causes of equipment failures and develop effective solutions.
Servant leader with strong team-building skills and a focus on team success, with the ability to motivate and develop a high-performing team.
Intuitive, adaptable, and creative, with excellent communication and interpersonal skills, with the ability to collaborate effectively with cross-functional teams.
Ability to:
Manage budgets and allocate resources effectively.
Collect, analyze, and present technical information to non-technical audiences.
Develop, track, and interpret metrics.
Manage multiple concurrent tasks in a fast-paced environment, effectively prioritize work, and deliver quality results.
Make appropriate decisions when confronted with obstacles, think about them before acting, and consistently resolve issues in creative and effective ways.
Demonstrate patience in a fast-changing environment.
Strong knowledge of:
Maintenance strategies, techniques, and best practices.
Computerized Maintenance Management Systems (CMMSs) and other relevant software applications.
TPM, RCM, LEAN, and process excellence programs.
Knowledge of:
Contract management principles and practices.
Applicable Federal, State, and local laws, rules, regulations, codes, and/or statutes.
Basic accounting and finance/budgeting principles and practices.
Microsoft Office Suite software including Access, Excel, Word, PowerPoint.
Must have working-level knowledge of the English language, including reading, writing, and speaking English.
Preferred Qualifications:
Expertise in integrating multiple, complex business and technical/engineering processes.
Proven project management skills, with the ability to prioritize tasks and meet deadlines in a fast-paced environment.
Prior experience with maintenance, design, and/or operation of facilities equipment in a high-tech manufacturing facility, such as a semiconductor, solar, or battery manufacturing site.
Prior experience with maintaining data and components for facilities, such as Scheduled Maintenance and Facilities Condition Assessment.
Alignment to Panasonic’s seven (7) core principles (contribution to society, fairness and honesty, cooperation and team spirit, untiring effort for improvement, courtesy and humility, adaptability, gratitude).
Preferred License(s):
- None
Preferred Certification(s):
- Certified Maintenance and Reliability Professional (CMRP) Certification.
Physical Demands
Physical Activities: Percentage of time (equaling 100%) during the normal workday the employee is required to:
Sit: 40%
Walk: 30%
Stand: 20%
Lift: 10%
Required Lifting and Carrying: Not required (0%), Occasional (1-33%), Frequent (34-66%, Continuous (67-100%)
For this position the required frequency is:
Up to 10 lbs.: Occasional
Up to 20 lbs.: Occasional
Up to 35 lbs.: Occasional
Team-lift only (over 35 lbs.): Occasional
About Us: At the heart of this visionary project, Panasonic is committed to manufacturing cutting-edge cylindrical lithium-ion cells that will power the future of electric mobility. These cells will be meticulously crafted to meet the growing demands of the automotive industry, supporting various electric vehicle manufacturers in their quest for eco-friendly transportation solutions.
This role presents a unique chance to be at the forefront of innovation, working within a forward-thinking organization that is committed to environmental responsibility and the advancement of green technology. Be a part of our mission to power the future and make a difference in the world of electric mobility with Panasonic!
Supplemental Information: Pre-employment drug testing is required. Due to the high volume of responses, we will only be able to respond to candidates of interest. All candidates must have valid authorization to work in the U.S. without restriction.
Panasonic is an Equal Opportunity employer, and all qualified applicants will receive consideration for employment without regard to race, color, religion, gender identity, sex, sexual orientation, national origin, disability status, protected veteran status, and any other characteristic protected by law. All qualified individuals are required to perform the essential functions of the job with or without reasonable accommodation.
Thank you for your interest in Panasonic Energy Corporation of North America.
REQ-147008