
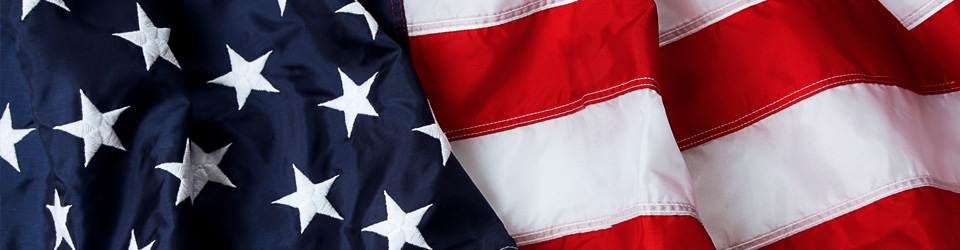
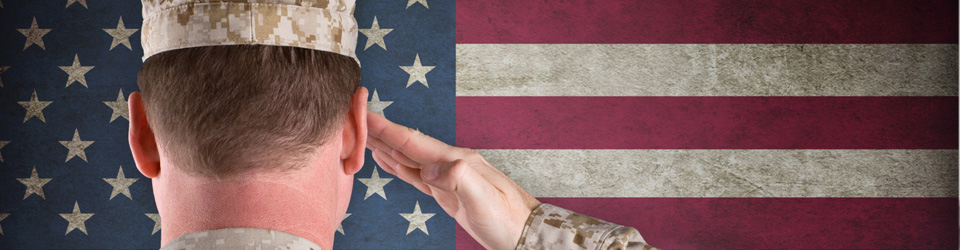
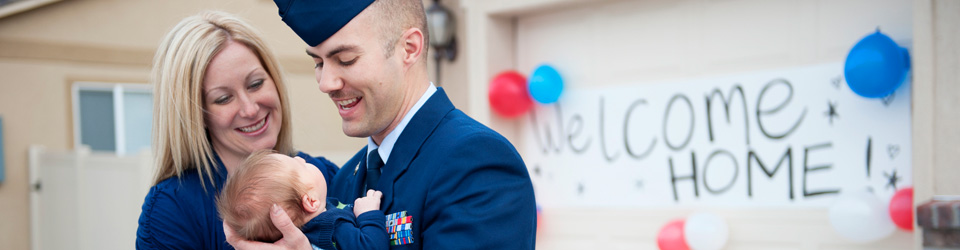
Job Information
Johnson Controls Tool and Die Supervisor - 1st Shift in Wichita, Kansas
Johnson Controls’ Wichita operation designs, builds and distributes around one million pieces of residential heating and cooling equipment every year. Johnson Controls Wichita builds and assembles some of the biggest HVAC brands in the industry, including York, Luxaire, Coleman, Champion and Guardian.
The primary manufacturing campus sits on 63 acres with a total of 1.3 million square feet. It has also translated into large employment growth in Wichita, where its workforce is around 1,600 employees which is up nearly 22 percent year over year. The Wichita manufacturing facility is the largest non-aircraft manufacturing plant in Wichita.
TOOL AND DIE SUPERVISOR POSITIONS ARE SALARIED; HOWEVER, THEY ARE STILL ELIGIBLE FOR STRAIGHT OVERTIME. IN ADDITION, THIS POSITION IS ELIGIBLE FOR A TARGETED 10% ANNUAL INCENTIVE BONUS. THE POSITION IS ALSO ELIGIBLE FOR A RELOCATION LUMP SUM ALLOWANCE.
THIS POSITION IS NOT ELIGIBLE FOR VISA SPONSORSHIP.
What you will do
The Tool and Die Supervisor will provide supervision, training and direction to toolmakers and set-up personnel on assigned shift to assure proper and timely preventative maintenance, set-up and repair of tooling.
How you will do it
Organize and schedule all work to be performed within the Tool Room including assigning personnel to projects and review finished work to assure compliance with maintenance, repair and set-up specifications and procedures.
Perform advanced troubleshooting when required techniques are beyond capabilities of assigned personnel.
Provide technical training to Toolmakers, Repair and Production team members.
Ensure that all tooling equipment is in good operating order; note malfunctions, schedule necessary maintenance or repair and communicate with follow-up across shifts to assure continuity of effort.
Collaborate with plant Engineering personnel in the resolution of complex technical problems and the introduction of new equipment and processes.
Conduct monitoring of experimental processes and equipment and perform other special project work as assigned.
Participate in hiring and leading the training and development of Tool and Die staff. Encourage, foster and enable highly effective problem-solving among staff.
Manage day to day work activity such as changeovers, PM schedule and repairs. Work with Scheduling and crew Supervisors for prioritization of projects.
Drive and maintain safety standards while being an active participant on the safety team.
Support tooling preventive maintenance program.
Create and maintain a Tooling reference tag required for each die.
Create and maintain standardization of die setup and teardown procedures. Apply learned best practices.
Provide focus, guidance and leadership in scrap reduction and uptime initiatives.
Lead production support of and identify improvements with die change processes in order to reduce or eliminate reoccurring problems and collaborate with Operations and Manufacturing Engineering on priority of activities related to those issues.
Teach, mentor, train and provide guidance to Tool and Die Makers equally across all shifts.
Liaise between Technicians, Tool Room Maintenance teams and Engineering to ensure efficient and effective problem resolution and to ascertain continuity of application.
Document, standardize and create procedures for repeatability, predictability and improved efficiency specific to related activities.
Maintain and create inventory system for MRO (maintenance repair) to ensure tools can be quickly repaired.
Participate in daily (PCC & MCC) production meetings to facilitate problem solving on day-to-day issues.
Maintain positive employee relations and adhere to Company policies and safety standards.
What we look for
Required:
Bachelor’s degree and a minimum of three (3) years of Tool and Die experience in a manufacturing environment or an Associate degree and a minimum eight (8) years of Tool and Die experience in a manufacturing environment or an equivalent combination of education and experience.
Minimum of three (3) years of experience working as a Tool and Die Supervisor in a manufacturing environment.
Experience developing and managing a robust Die maintenance and preventive maintenance program.
Ability to work 1st shift (6:00AM-3:30PM, Monday – Friday as well as weekend overtime as needed to support production).
Strong understanding of Milling and Machine Shop equipment as well a strong understanding of the mechanics of a Die, how it goes together and how to correct issues.
Ability to read blueprints.
Preferred:
CNC experience.
Experience with project and budget management.
Build your best future with the Johnson Controls team
As a global leader in smart, healthy and sustainable buildings, our mission is to reimagine the performance of buildings to serve people, places and the planet. Join a winning team that enables you to build your best future! Our teams are uniquely positioned to support a multitude of industries across the globe. You will have the opportunity to develop yourself through meaningful work projects and learning opportunities. We strive to provide our employees with an experience, focused on supporting their physical, financial, and emotional wellbeing. Become a member of the Johnson Controls family and thrive in an empowering company culture where your voice and ideas will be heard – your next great opportunity is just a few clicks away!
What we offer:
Competitive salary
Paid vacation/holidays/sick time
Comprehensive benefits package including 401K, medical, dental, and vision care – available day one
On the job/cross training opportunities
Encouraging and collaborative team environment
Dedication to safety through our Zero Harm policy
#WeAreJCI
Johnson Controls International plc. is an equal employment opportunity and affirmative action employer and all qualified applicants will receive consideration for employment without regard to race, color, religion, sex, national origin, age, protected veteran status, genetic information, sexual orientation, gender identity, status as a qualified individual with a disability or any other characteristic protected by law. To view more information about your equal opportunity and non-discrimination rights as a candidate, visit EEO is the Law (https://www.johnsoncontrols.com/-/media/jci/careers/landing/eeo-is-the-law.pdf) . If you are an individual with a disability and you require an accommodation during the application process, please visit here.